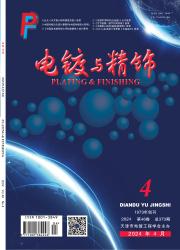
电镀用高纯氧化铜的合成方法
随着微电子技术的飞速发展,印制电路板(PCB)制造向多层化、积层化、功能化和集成化方向迅速发展[1]。在PCB制造工艺中,传统的镀铜工艺是采用可溶性阳极工艺,以磷铜球作为阳极并补充铜源,但是在电镀的过程中会产生阳极泥并会进行富集,最后导致电镀层的不良,因此传统的可溶性阳极镀铜工艺有工艺温度性差,效率低等缺点[2]。
目前PCB制造业中,开始逐渐采用水平电镀工艺,线路板水平电镀铜工艺阳极不可溶性的这一特性决定了生产工艺中需要间歇补充铜离子来维持镀液中的铜离子浓度。现在PCB业界水平电镀酸铜体系中铜离子的补充主要依靠氧化铜来完成,氧化铜粉应用于线路板水平电镀铜的时代即将来临[3]。用氧化铜代替磷铜球作为铜源,可以中和电镀过程中产生的H+,保证电镀液pH值的稳定,因此,该工艺中要求电镀级氧化铜有较高的活性,即在电镀液中能够快速溶解,并且要求有较高的纯度和较低的杂质含量。
目前市场通用的分析纯氧化铜试剂执行的是国标GB/T 674-2003,其纯度和杂质含量远远不能满足电镀使用要求。本文合成的高纯氧化铜,纯度在99.3%以上,杂质含量也远远低于分析纯标准,达到了电镀用氧化铜高纯度、低杂质的要求。
1 实验部分
1.1 主要仪器与试剂
硝酸铜、碳酸氢铵、铜粉(均为分析纯试剂)。
岛津X射线衍射仪XRD-6000、HK-8100型ICP-AES、PTY-C2000电子天平、电热套、高温炉等。
1.2 实验原理
硝酸铜与碳酸氢铵制备碱式碳酸铜,碱式碳酸铜经洗涤、干燥后,焙烧制备氧化铜。所涉及的主要化学反应如下:
1.3 实验内容
1.3.1 碱式碳酸铜的制备
将250g分析纯硝酸铜溶于1000g纯水中,搅拌溶解完全,制成1mol·L-1的溶液,加入铜粉,加热至60~80℃保温搅拌0.5h除氯,用活性炭过滤清亮,得溶液a。将180g分析纯碳酸氢铵溶于2200g的纯水中,搅拌溶解完全,制成1mol·L-1的溶液,用活性炭过滤至清亮,得溶液b。将溶液a加热至60~80℃,缓慢搅拌下,将溶液b滴加入溶液a,有少量沉淀生成时,停止滴加,继续保温反应30min,待沉淀晶核增大后,继续滴加反应,反应终点pH值控制在6~6.7。将上述反应溶液保温反应4h,静置过夜后,过滤,沉淀用纯水充分洗涤后,于80℃下干燥6h,得绿色固体碱式碳酸铜。
1.3.2 氧化铜的制备
将合成好的碱式碳酸铜55g置入1L瓷坩埚中,于高温炉中800~830℃焙烧6h,即得黑色粉末氧化铜。
2 结果与讨论
2.1 合成碱式碳酸铜的原料选择
选择硝酸铜与碳酸氢铵为原料合成碱式碳酸铜,其主要原因是易获得较纯的硝酸铜与碳酸氢铵,副产物中NO3-与NH4+较易洗去或受热时分解去除,从而避免影响氧化铜质量。另外,在合成过程中较易调控pH值在适当范围,物料损失较小,合成的碱式碳酸铜颗粒较大,易清洗,纯水损耗小。
2.2 氯化物杂质的控制
高纯氧化铜的指标要求氯化物含量小于10×10-6。原料中含有的氯化物在反应过程中可能生成碱式氯化铜,而碱式氯化铜在灼烧时不分解成氧化铜,导致最终产品中氯化物含量超标,所以需在合成碱式碳酸铜之前除去原料中的氯化物。可采用铜粉除氯法,即将铜粉加入硝酸铜溶液中,保温搅拌0.5h,沉淀滤去后再合成碱式碳酸铜。该法简便易操作且除氯效果明显,其反应原理如下:
单质铜与二价铜离子反应生成亚铜离子,亚铜离子与氯离子结合生成氯化亚铜,氯化亚铜微溶于水,可过滤除去,达到去除氯化物的目的。
2.3 其它反应条件的考察
2.3.1 碱式碳酸铜的制备
由硝酸铜与碳酸氢铵制备碱式碳酸铜的过程中,主要考察了二者投料摩尔比与滴加方式对产品外观的影响。通过一系列实验证明,当硝酸铜、碳酸氢铵溶液浓度为1mol·L-1,摩尔比 n硝酸铜∶ n碳酸氢铵=1∶ 2.2且采用“正加方式”(即将碳酸氢铵溶液加入硝酸铜溶液中)时,溶液反应终点pH值在6~6.7,合成的碱式碳酸铜颜色为深绿色,结晶颗粒大,易清洗,下一步焙烧出的氧化铜粉末色泽好、颜色均匀,质量达标率高。
2.3.2 氧化铜的制备
2.3.2.1 焙烧温度对氧化铜含量的影响
碱式碳酸铜加热分解成氧化铜,提高温度有利于分解的进行。其它反应条件不变,反应时间为6h,改变焙烧温度,其对产物氧化铜含量的影响如图1所示。焙烧温度低于800℃,碱式碳酸铜分解不完全,氧化铜含量较低;温度提高至800℃,碱式碳酸铜分解比较完全,氧化铜含量在99.3%以上;继续升温,含量变化不大,所以选择800℃为最佳反应温度。
下一篇:没有了